PE Plastic Film Blowing Machine Small Laboratory Film Blowing Equipment
Product introduce
This machine is the main equipment of the film blowing machine, and its function is to plasticize and extrude polymer. The screw and barrel are both made of 38CrMoAl alloy steel, and the surface is treated with processes such as nitriding and ultra precision honing. This machine is equipped with 3 zones for heating, and 2 zones for heating the mold head and mold mouth, with a total of 5 zones for heating.
The extruder screw is divided into three sections: feeding section, melting section, and homogenizing section.
Characteristic
1. At the inlet of the feeding section, set the heating temperature low to prevent the raw material from sticking and blocking the material outlet. In addition, the resin in the feeding section is continuously compressed, and the air will be discharged from the feeding port upside down. Although the feeding port is not heated, it will transfer heat through the machine barrel. Therefore, the temperature of the feeding port can be set to around 50-90℃.
2. In the melting section, the viscous flow temperature is reached before melting. For crystalline resins, the viscous flow temperature is equal to the melting point temperature. Then, by continuously compressing and increasing the melting layer, it is necessary to continuously increase the temperature in order to make the length of resin molecular chains unequal, so that polymers with different thermal motion energies can melt successively.
3. In the homogenization stage, the temperature is constant. Because this section is an input melt for remelting homogenization and quantitative constant pressure and constant temperature. In summary, the temperature control of each section of the extruder is an important factor in pipe blank extrusion. Usually, the temperature of the plastic gradually increases along the direction from the barrel to the head mold, and the temperature change is linear. The temperature in Zone 1<Zone 2<Zone 3<Zone 4<Zone 5 is equal to the melting point temperature.
The screw speed of this machine is variable frequency speed regulation. The speed directly affects the quality of film blowing. Usually, if the screw speed is too fast and the temperature is set too high, the shear force is large, which can easily cause plastic decomposition and poor cooling of the film tube. This makes it difficult to stabilize the film diameter, resulting in uneven diameter and wall thickness of the blown film bubbles, leading to the formation of "long neck" unstable film bubbles. Therefore, the speed of a single screw extruder and the temperature settings of the five heating zones of the body are particularly important.
Specification
Traction roller size |
Ø 80×L350mm |
Die diameter |
Ø 25 |
Traction winding speed |
0.5~5m/min adjustable |
Film diameter |
150mm |
Traction motor |
0.75 |
Winding torque motor |
3.5N. M |
Fan |
0.25KW |
Main motor power |
2.2KW |
Traction motor power |
0.75KW |
Host frequency converter |
2.2 kW |
Heating power |
5KW |
External wiring cable |
4 wires, 6 square meters |
Screw diameter |
25 or 28 |
Screw length to diameter ratio |
1:30 or 1:34 |
Die size |
3 points |
Machine size |
600X1200X2450 |
Wind ring size |
420mm |
Volume |
600X1200X2450 (W×D×H) mm |
Power supply |
3-phase. AC380V.15A |
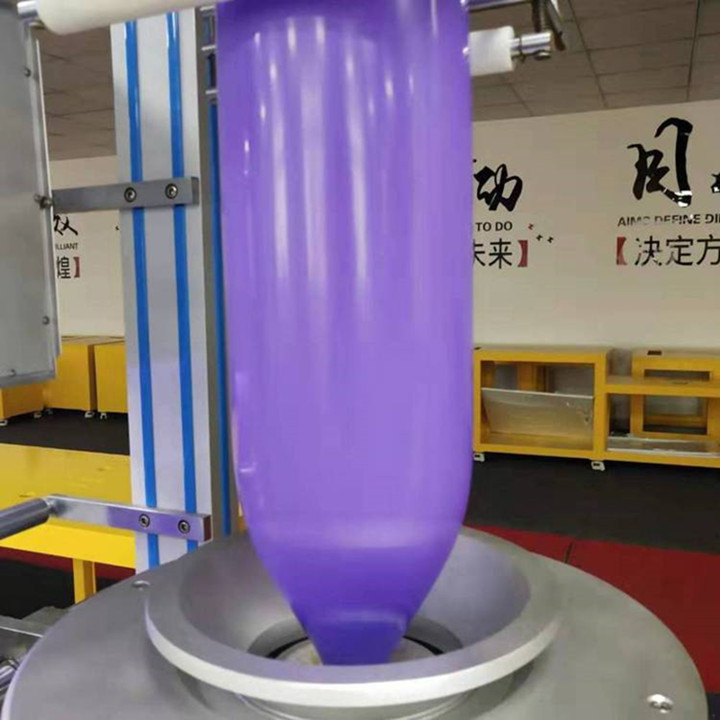